The rapid growth of industry since the turn of the century, as well as the widespread use of machinery powered by motive power, necessitated a continuing search for more efficient procedures. Until around 60-65 years ago, industrial tasks required dense labour, which not only necessitated a large workforce, but also had an impact on quality, precision, and repeatability, as well as higher prices and lower output.
To what extent is this true? With a simple example, you can see what it means. Many people who work in a machine shop, for example, are familiar with one of the most basic industrial tasks: drilling holes in sheet metal with a hand drill. To do so, the operator must perform a number of tasks, including placing the sheet on the drill table, inserting a drill bit into the chuck and securing it to the spindle, changing the rotation speed with the pulleys, activating the spindle, and operating the lever, or advance wheel, to direct the drill towards the sheet to be machined.
Consider the practicality of such a technique in an industrial setting, where hundreds of holes must be drilled in hundreds of sheets in the shortest possible time, at the lowest possible cost, and with the highest possible quality. That was the difficulty that companies faced in the early half of the twentieth century, and as a result, technological improvements accelerated toward the automation of production processes, or the invention of equipment capable of doing all of an operator’s manual tasks automatically.
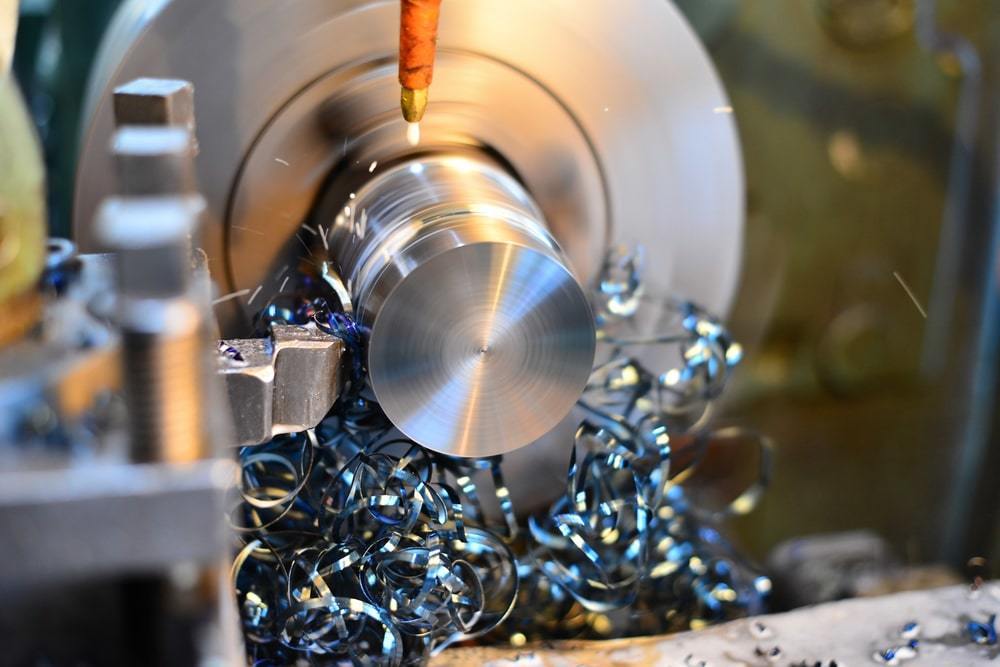
What Is CNC And How Is a CNC Machine Collected?
Computerized arithmetical control, to put it simply, happens to be the use of a computer to control and monitor the actions of a machine tool. Milling machine, lathe, grinding machine, laser cutting machine, water jet or EDM, stamping machine, press, robotic arm, and so on are examples of static and portable machine tools. Large machines have a built-in computer, and the majority feature a sophisticated feedback system that constantly checks and changes the cutting tool’s speed and location. In workshops, less demanding machines allow for the use of an external personal computer. To move the machine axes in a controlled manner and perform the planned movements, the large cnc machining malaysia controller works with a sequence of motors (servo motors and/or stepper motors), as well as drive components.
A CNC Machine, Therefore, Consists Of Six Main Elements:
- Input device
- Machine tool
- Control unit or controller
- Drive system
- Monitor
- Feedback devices (only in systems with servo motors)
How Does A CNC Machine Work?
As seen in the previous diagram, the CNC machine controller receives instructions from the computer (in the form of G codes and M codes) and, using its own software, translates those instructions into electrical impulses that are used to activate the motors. They will then turn on the driving system.
a) Motion Management
A common feature of all CNC machines is that they have two or more programmable motion directions known as axes. An axis of motion can be either linear (in a straight line) or rotary (in a circular motion) (in a circular path). The number of axes a CNC machine has is one of the initial characteristics that indicates its complexity. In general, the more axes there are, the more complicated the system becomes.
A CNC machine’s axes are required to generate the movements required throughout the production process. Continuing with the industrial drill as an example, the axes would set the tool on the hole to be machined (on two axes) and perform the operation (with the third axis). Letters are used to identify the axis. X, Y, and Z are the most popular names for linear axes, while A, B, and C are the most common names for rotational axes.